Choosing the most sustainable options for your boat can leave you feeling confused, but don’t worry, you’re in good company.…
Are wooden boat the answer to environmentally responsible yachting?
With intensifying focus on the environmental impact of GRP boats, Theo Stocker looks at the latest wooden boats to see if there is a better way
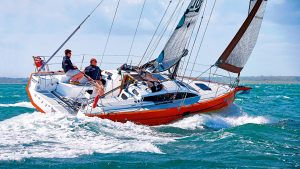
Boatbuilding as we know it is not a sustainable process. The dawn of mass production GRP boats from the 1960s onwards fuelled an explosion in sailing participation and boat ownership. Rather than building each boat from scratch, as wooden boats have been since time immemorial, GRP boats can be laminated and popped out of a mould at speed, their fair lines cloned from one single plug tens or hundreds of times.
The cost of buying boats tumbled and allowed many to get on the water for the first time, and for that, fibreglass is to be lauded – a miracle material that is immensely strong, light, robust and virtually maintenance free.
Boat building is big business, with an estimated six million leisure boats now bobbing around in Europe and 10,000 new boats reportedly being pumped out every year in the UK alone. The problem, environmentally speaking, is twofold: building GRP boats produces a lot of CO2, and the boats, once at the end of their lives, never biodegrade, and recycling GRP is extremely difficult.
New technologies are emerging all the time, from bio resins and natural fibre to composites that can be returned to their original states and remade into new objects. But old technologies also remain relevant – in particular, wood.
While traditional boatbuilding remains a live skill, it is on modern construction techniques that any future in wooden boats really lies, merging modern resins and plywoods with traditional materials to produce complex, modern, lightweight shapes, but with a much lower impact both in build and at end of life.
I spoke to three of the leading yards building modern boats in wood today to find out about the latest innovations in wooden boat building, and how they are constantly working to make boat building more sustainable, as well as more affordable and accessible.
Article continues below…
ON TEST: Spirit 44e – the sustainable future of sailing?
A wooden boat that blazes a trail for modern technology and sustainability sounds too good to be true. Theo Stocker…
These were Spirit Yachts in Ipswich, building modern classics from 30ft daysailers up to 111ft superyachts, Swallow Yachts in Cardigan Bay, which builds small but rugged trailer sailers, cruisers and motorboats, and RM Yachts in France, which builds a sporty range of offshore and bluewater cruising yachts.
It has taken time for the sailing public to understand the difference between modern and traditional wooden boat building, however.
‘Modern wooden boatbuilding is a world apart from traditional wooden boat building,’ explained Matt Newland, owner of Swallow Yachts. ‘When we started in 1995, we had to spend a lot of time explaining to sailors that a modern ply epoxy boat is completely dry and virtually as low maintenance as a GRP boat.
‘It used to be about 30% more expensive to build a boat in plywood than in GRP, even though it would come out just as stiff and far lighter. That’s come down now though, and by the time you get to a 30ft boat, the cost works out about the same.’
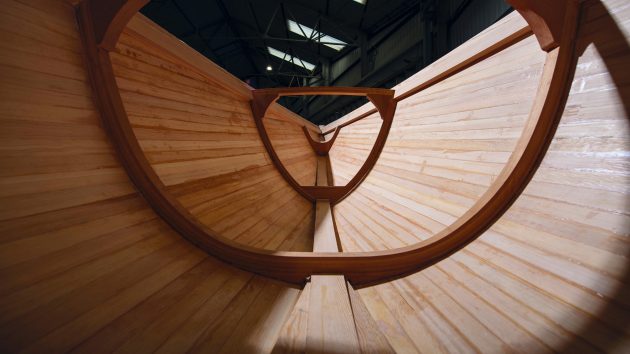
Strip planks are secured to laminated hull frames to create the basic shape of a Spirit yacht. Photo: Spirit Yachts/Mike Bowden
Wooden boats also have a much lower environmental impact, said Newland. ‘Wood is definitely more sustainable than GRP, according to the Life Cycle Analysis that we completed using the Marine Shift 360 tool. In fact, for a 30ft boat, we were getting a reduction of just over 50% (total CO2 emissions) when compared to a boat of similar size built with glass fibres and polyester/vinylester resins. Carbon fibre, on the other hand, is just about the worst thing you can build a boat in, from an environmental point of view.’
Wood sourcing
At Spirit Yachts, sustainability has been at the heart of what the yard does since its inception, and the company continues to work to find ways to reduce its impact. That starts with timber selection for yard manager Adrian Gooderham, who personally selects each piece of wood the yard buys, ensuring it is free from imperfections that would send it to the scrap heap.
This is bought from their local supplier, Thorogoods, minimising the distance Adrian or the timber has to travel. Planning ahead, enough timber is ordered for multiple boats to keep deliveries to a minimum – the last Sipo log the yard used went into the five most recent boats to be built.
And when boats come in for refit, timber and offcuts already in stock are used where possible.
‘Our Sipo comes from central Africa, while Douglas fir and yellow cedar come from Canada, and walnut from the USA,’ explained Gooderham. ‘The growers are doing a good job of sustainable forestry, planting two trees for every one felled to ensure forests are increasing rather than decreasing in size. They don’t clear fell either, but leave the big, slow-grown trees in place.’
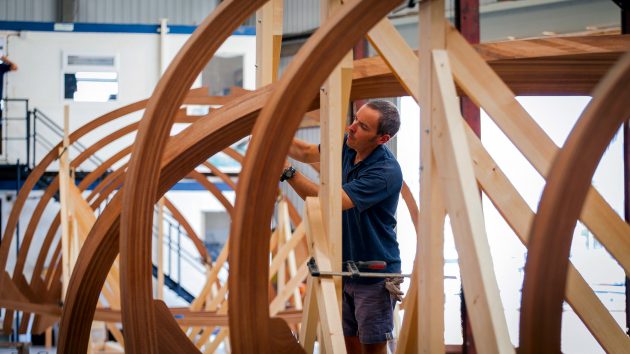
Frames are secured to a timber strongback and braced with pine. The timber is also reused multiple times, before being donated to a local college. Photo: Spirit Yachts/Mike Bowden
Teak wood is no longer used in Spirit’s boats due to the decimation of forests in Myanmar (as well as the political sanctions there), and after a brief foray into thermally modified timber, decks are now laid in Douglas fir, a straight-grained, durable and knot-free timber that turns a similar silver grey to teak.
The wood is then used in a way that minimises waste – interior furniture parts are cut from sheet ply by a CNC cutting machine, allowing each sheet to be used in the most efficient and precise way to get more from it, with cuts that wouldn’t be possible by hand. Any timber that can be reused is collected, and anything else that’s left over is donated to a local college for woodworking courses.
Over in France, RM Yachts, which are built in plywood, buys wood that has already been transformed into an engineered product and has even been CNC-cut into the constituent parts needed for each boat, but it still keeps a close eye on how the wood is sourced.
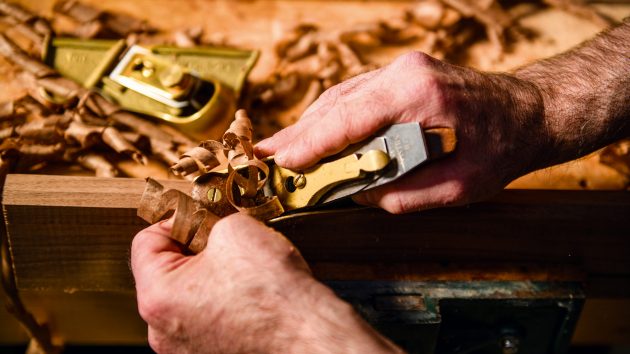
Traditional joinery skills are still much in evidence at Spirit. Photo: Spirit Yachts/Waterline Media
César Dohy, commercial director of RM Yachts, explains: ‘Okoumé plywood behaves exceptionally well when it comes to humidity or even salt water. The quality of the glues, which has been extensively tested in particularly demanding tests (72 hours in boiling water, etc.), means that our plywood can be used for “ultimate” applications, such as the whole outside shell of our boats. Okoumé plywood is also a renewable, available and abundant resource.
‘French plywood manufacturers are concerned about preserving resources, both in terms of quantity and quality, and rely on the eco-certification of forest basins (PEFC or FSC marking), thereby adopting a sustainable approach to manufacturing using wood from sustainably managed forests.
‘Our plywood manufacturer is regularly audited to ensure that they comply with the strict specifications of the European Union Timber Regulation (EUTR), which applies to all operators and verifies the legality of the timber.’
Swallow Yachts takes a similar approach, says Newland. ‘The impacts of building in wood vary according to where you are taking your wood from. Swallow only buy from FSC sources, which gives some degree of environmental credibility.
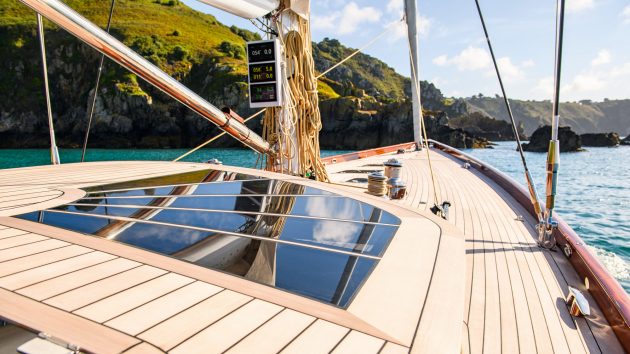
Douglas fir, though a softwood, is a traditional decking timber that is hardwearing, straight grained and ages well, now being used by Spirit.
‘New products are coming out all the time claiming to replace old growth hardwoods such as teak and iroko with treated alternatives that are grown sustainably,’ Newland continues.
‘The company has not had a good experience with most of these, as the treatment process significantly alters the long cellulose fibres that give wood its great strength. We are hopeful that one day someone will crack this problem, but at the present time we are proceeding with extreme caution.
‘Don’t forget though, that wood is basically carbon sucked from the air, via the magic of photosynthesis, reducing atmospheric CO2. So I see creating demand for wood as a force for good.
‘We use marine plywood using African Okoumé for the outer skin but for the decks and internal structure we use a treated poplar plywood called DuraPly from the Spanish company Garnica,’ says Newland.
‘This is a big environmental win for us as the wood is more than up to requirements in these parts of the boat, and poplar is fast-growing, and preferable to using tropical hardwoods. This type of wood now makes up around 80-85% of our boats, with only 15-20% being Okoumé hardwood ply.’
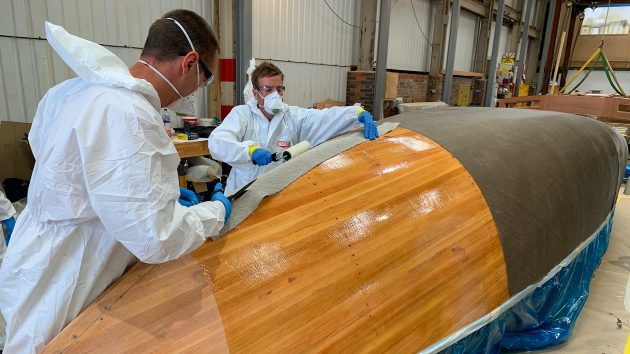
Two Spirit 30s have now been build with flax and bio-resin outer skins, doing away with the veneer. Photo: Spirit Yachts/Mike Bowden
Resins & glues
Processes are changing too. Resins and vacuum infusion is notoriously wasteful, as excess resin cannot be reused, and the plastic sheeting for the infusion bagging is also single-use. While this is hard to get around, Spirit Yachts has switched vacuum bagging material to DTC’s carbon-neutral vacuum bag/bleed film and breather cloth.
‘This is actually cheaper than the product we were using before and buying it in bulk helps too,’ added Gooderham. Even the pots in which the resin is mixed, which used to be used once and thrown away, are saved and the epoxy removed once set and then reused multiple times.
Environmental concerns
‘Our boats do contain synthetic resins – we exclusively use the West System with their 105 epoxy, and they are always working hard on meeting the latest standards and finding ways of reducing the product’s environmental impact.
‘We use epoxy to create laminated shapes, to glue veneers in place, and when sheathing the hulls. While these resins are not bio products, there is very little of them in our boats compared to a moulded GRP boat.
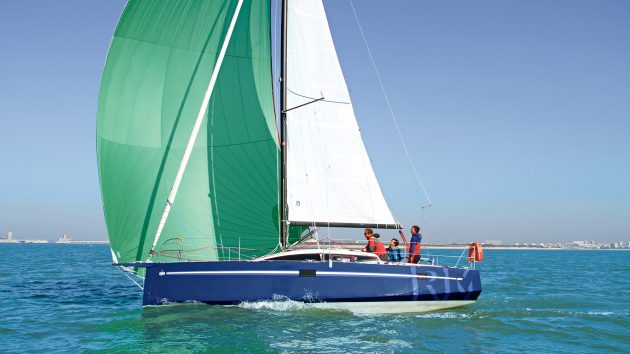
RM Yachts operates a ‘zero non-recovered waste’ approach to building its boats. Photo: RM Yachts
‘In theory, at the end of the boat’s life, it wouldn’t be difficult to remove this outer skin and to recycle the rest of the boat. In 30 years of Spirit Yachts, however, none of our boats have ever been scrapped.
‘Being predominantly made of wood, they are infinitely repairable, which GRP boats are not, and they would also be easier to break down and dispose of.’
Swallow Yachts in Wales has also been experimenting with bio-resins, and has adopted them fairly widely on board already. Matt Newland explained, ‘We build our wood epoxy Whisper 300 with bio resins, which give a slightly more favourable life cycle assessment measure. We use West Pro-Set on the inside of the boat where we find it sets perfectly well in areas not exposed to UV, though we still use standard post-cured West System epoxy on the outside of the boat where a UV resistant and stable base is needed.’
Rather than specifically organic materials, RM Yachts is focusing on recyclable resins. ‘The next industrial development in wooden boat building in the future will most certainly be the use of thermoplastic resins in order to recycle boats in a more responsible manner. That will certainly reduce the impact of the raw materials, the recycling process, and therefore our company operations,’ said Dohy.
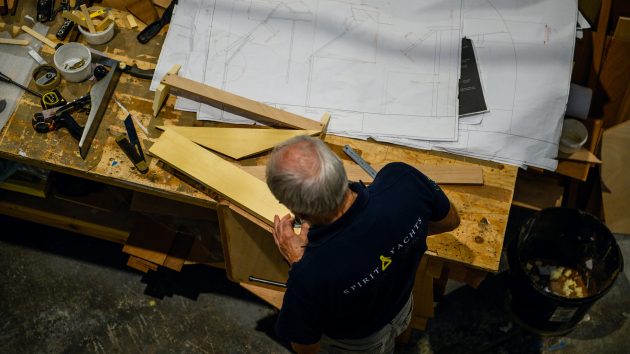
Offcuts from one project are used as smaller parts in another. Photo: Spirit Yachts/Waterline Media
These are resins that can be heated to effectively ‘melt’ the resin out of the reinforcing fibres, leaving both undamaged and in their original state. Beneteau Group has trialled this technology, building the new Beneteau First 44 and the Jeanneau Sun Fast 30 One Design in recyclable Elium resin, made by Arkea.
Supply chains
While not strictly related to building in wood, Spirit Yachts has applied the same approach to much of the rest of its supply chains. Raw materials and parts are sourced as locally as possible, from electrical switch panels and solar panels – all made in the UK – and recycled materials, such as recycled PVC cable ducting, are used wherever possible.
Waste from both the boats and the general yard, whether it’s wiring offcuts, toilet rolls or food waste, are separated, reused, donated (such as old sails and ropes to local schools for projects), or recycled.
Plastic is minimised with cardboard and brown paper sheeting used for protecting boats being worked on rather than single-use plastic sheeting, and paint trays, previously single-use plastic, are now sourced in biodegradable cane sugar pulp, which are also reusable rather than single-use.
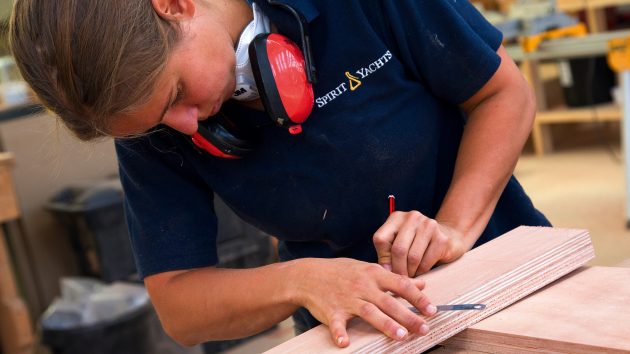
Top quality materials and careful stock management minimise waste of valuable raw materials. Photo: Spirit Yachts/Mike Bowden
The net result is a significant reduction in landfill waste – six years ago Spirit Yachts had a skip collection once a week, now it’s once every three weeks.
Of course, some of this costs more, but it isn’t always more expensive, explained Gooderham: ‘Sourcing materials locally saves on shipping and delivery costs. The parts we fit also hopefully last longer, both as a way of avoiding replacement costs and reducing the boat’s lifespan carbon footprint.
‘For example, high-quality tinned cables are more corrosion resistant; we’ve worked hard to remove metal from seawater systems to eliminate the waste of damaged parts, and we’ve switched from zinc to aluminium anodes. Push-fit technology has eliminated leaks of antifreeze from aircon systems, and all of the engines and generators we fit are now certified and warranted to run on HVO.’
At RM Yachts, suppliers are as local to the yard as possible. ‘Strategically, our supply chain and logistics are done in a very small circle,’ explains Dohy. ‘We have our major suppliers within 80 miles of the yard, such as the plywood manufacturer, sailmaker, mast maker, upholsterer, plumbing, resins, etc. It certainly has a big impact on our boat building process.
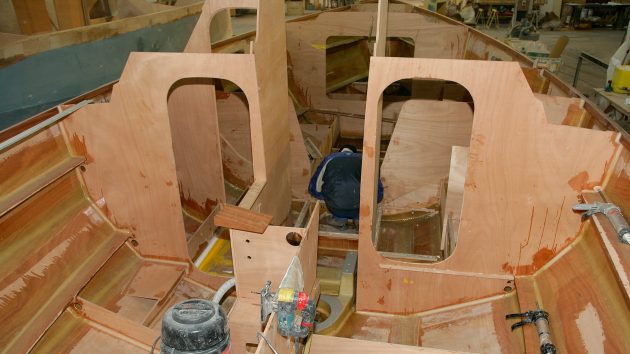
All joins and internal bulkheads are laminated in place on an RM yacht. Photo: Graham Snook/YM
‘Ongoing investment enables us to reduce the environmental impact of production and maintain long-term jobs and the economic activity needed in the local area. Manufacturing by products are recovered in the form of fuel (wood-fired boilers) which provide the energy needed for the manufacturing process. This is the “zero non-recovered waste” approach.’
Swallow Yachts similarly uses waste material to create energy for the boatyard. Each workshop is heated with a sawdust burner which is fired from in-house waste, saved in a large shipping container in the summer then burned in winter. ‘This year we got to mid February before we had to buy more firewood,’ said Newland.
Demand
So are wooden boats the future? It all depends on prospective buyers, says Spirit Yacht’s Gooderham. ‘To a large extent, the sustainability of boat-building is based on customer demand.
We can’t upscale much more at the site we’re currently at, but if there’s demand, then other companies might see an opportunity in building in wood. We certainly feel that our approach is much more sustainable than mass-production GRP building.
‘Our customers come to us because they are looking for something that is a bit different and not built in GRP,’ Gooderham continues. ‘It helps that our boats are beautiful and have some soul to them. We are always striving to find ways to build boats that are as easy to maintain as fibreglass, so there is no additional burden to owning a wooden boat.’
Enjoyed reading this?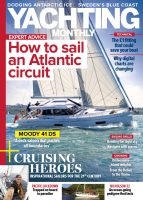
A subscription to Yachting Monthly magazine costs around 40% less than the cover price.
Print and digital editions are available through Magazines Direct – where you can also find the latest deals.
YM is packed with information to help you get the most from your time on the water.
-
-
- Take your seamanship to the next level with tips, advice and skills from our experts
- Impartial in-depth reviews of the latest yachts and equipment
- Cruising guides to help you reach those dream destinations
-
Follow us on Facebook, Twitter and Instagram.
The post Are wooden boat the answer to environmentally responsible yachting? appeared first on Yachting Monthly.